
(3)

数值模拟共设置14组不同尺寸缺陷拉伸实验,具体缺陷尺寸见表2. 表2中:l为实际长度;a为实际深度; 环向投影尺寸C为缺陷沿管道环向投影最长距离; 纵向投影尺寸lm为缺陷沿管道轴向投影最长距离; 相对长度L、相对宽度W与相对深度A是按照环向投影长度、纵向投影长度与实际深度计算得到. 根据刘维洋等[15]、梁涛[16]在研究中发现缺陷宽度变化对管道极限承载力影响较小,故将宽度w设为定值,w=4 mm. 将14组最大缺陷尺寸d=5.6 mm,l=20 mm代入式(2)~(3)计算,得到Lm=50.21 mm,大于最大纵向投影长度lm,故含此尺寸缺陷管道属于第三类,表明缺陷尺寸设计合理.
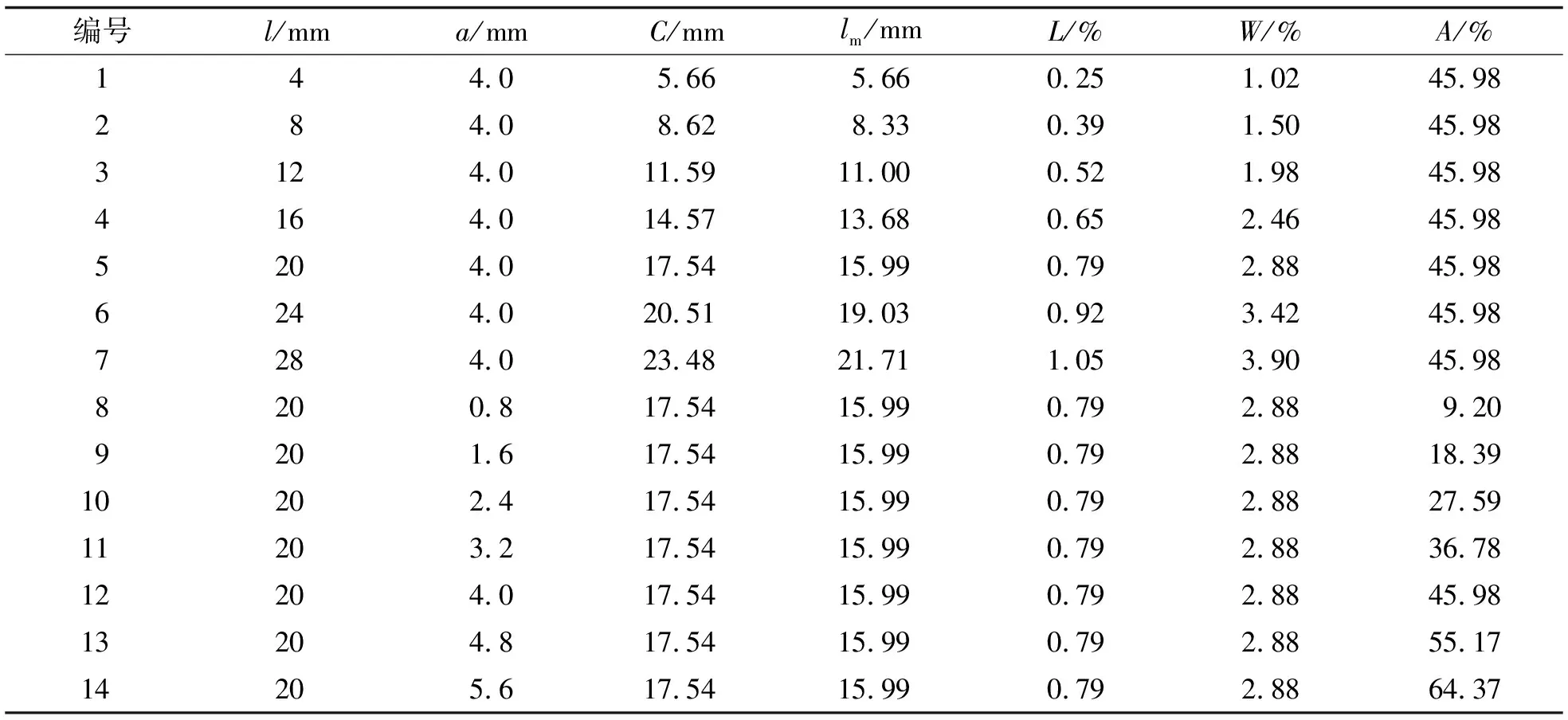
表2 缺陷尺寸参数
2.2 有限元模型建立
宽板从中心到两侧分为3部分:减宽段,过渡段与夹持段. 根据文献[17]中规定:减宽段宽度与管道壁厚的比值等于6~10,减宽段长度与宽度的比值须大于等于2. 根据文献[18]中规定:夹持段宽度须大于1.25倍的减宽段宽度; 过渡弧半径须大于等于0.3倍的宽板减宽段宽度. 本文研究管道壁厚为8.7 mm,故设置宽板减宽段宽度设为56 mm,长度为120 mm; 夹持段宽度取76 mm,长度取50 mm; 过渡段中过渡弧半径取30 mm,计算的宽板过渡段宽10 mm,长30 mm,如图1所示.
利用ABAQUS的CAE模块,建立宽板试件模型, 管道网格单元选择C3D8R(八节点线性减缩积分六面体单元). 对重点研究区域的网格划分采用细网格,而对非重点研究区域网格划分采用粗网格,网格划分结果如图2所示.

图1 宽板尺寸图(单位:mm)Fig.1 Wide plate demensions(unit: mm)

图2 管道宽板网格Fig.2 Pipe wide plate grid
2.3 宽板与全尺寸管道在拉应力下对比分析
建立含相同尺寸参数与位置参数的半球形缺陷的宽板模型及全尺寸管道模型. 半球形缺陷直径10 mm,位于宽板及全尺寸管道中心部位,且与焊缝相距2 mm; 全尺寸螺旋焊管的长度为500 mm,外径711 mm,壁厚8.7 mm,同时对宽板和全尺寸管道施加5 mm的轴向位移载荷. 缺陷底部应力分布及变化曲线, 如图3所示.
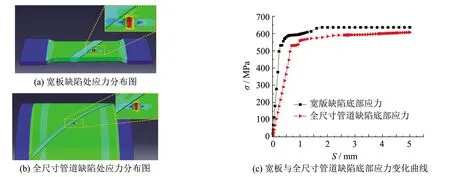
图3 宽板与全尺寸管道缺陷底部应力分布及变化曲线Fig.3 The stress distribution and change curve at the bottom of the defect of wide plate and full-size pipeline
从图3可看出:宽板与全尺寸管道缺陷处的应力分布相同,应力集中部位均在缺陷纵轴两侧,而缺陷横轴两侧应力较小. 宽板与全尺寸管道焊缝处缺陷底部应力变化趋势相同,表明通过宽板模型研究缺陷处应力变化与裂纹扩展具有合理性.
2.4 不同长度与不同深度缺陷处裂纹萌生规律分析
对含不同长度与不同深度焊缝处缺陷的管道宽板进行建模,共14组宽板模型. 通过对宽板施加轴向拉伸应力,得到不同长度与不同深度缺陷处裂纹萌生时对应的位移载荷和萌生尖端应变, 分别如图4、图5.

图4 位移载荷Fig.4 Displacement loads corresponding

图5 尖端应变Fig.5 Tip strains
从图4可以看出,随着缺陷长度或者深度的增加,不同长度和不同深度缺陷处裂纹萌生所需位移载荷逐渐减小,表明含缺陷宽板的承载力也在逐渐减小,并且减小的趋势逐渐变缓. 当缺陷相对长度大于0.79以及缺陷相对深度大于45.98时,位移载荷减小呈变缓趋势,缺陷长度参数和深度参数对宽板裂纹萌生的影响逐渐减小. 结合图5缺陷处裂纹萌生尖端应变规律可知,当缺陷相对长度为0.79(实际长度为20 mm)和相对深度为45.98(实际深度为4 mm)时,缺陷对裂纹萌生的影响较大.
3 应变与裂纹扩展实验分析
3.1 宽板拉伸试件制备
通过分析缺陷尺寸参数对裂纹萌生的影响,选取影响最大的缺陷尺寸(长20 mm,宽4 mm,深4 mm)进行拉伸实验. 为研究双点缺陷对裂纹的影响,设置A、B、C共3块宽板. A为实验对照组,为不含焊缝处缺陷的管道宽板; B为含单个焊缝处缺陷的管道宽板,缺陷紧贴焊缝上侧,相对焊缝上侧中线向左平移4 mm. C为含两个焊缝处缺陷的管道宽板,缺陷均在焊缝的上侧,分别为两个缺陷与焊缝中线呈轴对称,相对焊缝上侧中线左右偏移4 mm.
宽板试件首先采用气割的方法从全尺寸螺旋焊管上切割长方形宽板,再通过线切割的方法加工成设计尺寸. 经过切割后的管道宽板已经成型,随后利用电火花刻伤技术,在管道宽板上预制缺陷. 然后通过PWS-500电液伺服试验机对每块管道宽板两侧的夹持端进行校平工作. 最后利用脱漆剂、钢丝砂轮等工具对宽板进行去漆打磨等二次加工,且保证材料表面不出现二次损伤.
3.2 实验过程

图6 宽板应变片布点图Fig.6 Wide-plate strain gauge layout diagram
拉伸实验过程通过拉伸试验机进行,通过在宽板焊缝及缺陷周围布置大量的应变片,监测在轴向拉力作用下宽板表面以及缺陷周围的应变情况. 本次实验选用500 kN拉伸试验机,对宽板施加恒定速度为0.3 mm·min-1的位移载荷. 通过使用电阻式应变片监测宽板表面应变变化,A、B、C宽板布点方案如图6所示.
实验选用30通道静态应变采集分析系统,采用四分之一桥三线制的接线方法,用以监测并记录应变片数据. 根据宽板拉伸实验的材料属性与应变采集分析系统的特征参数,选用应变片型号为120-5AA金属应变片. 通过在宽板前后架设视频监测摄像头,并在宽板表面固定网格为5 mm的透明刻度板,实时捕捉宽板缺陷处的裂纹扩展尺寸变化过程.
3.3 含缺陷宽板焊缝处应力应变分析
在进行点位处应变分析时,均采用点位编号分析,例如,A-1表示宽板A中的1号点位. 图7、图8所示为A、B、C宽板焊缝处上、下侧应变对比分析图.
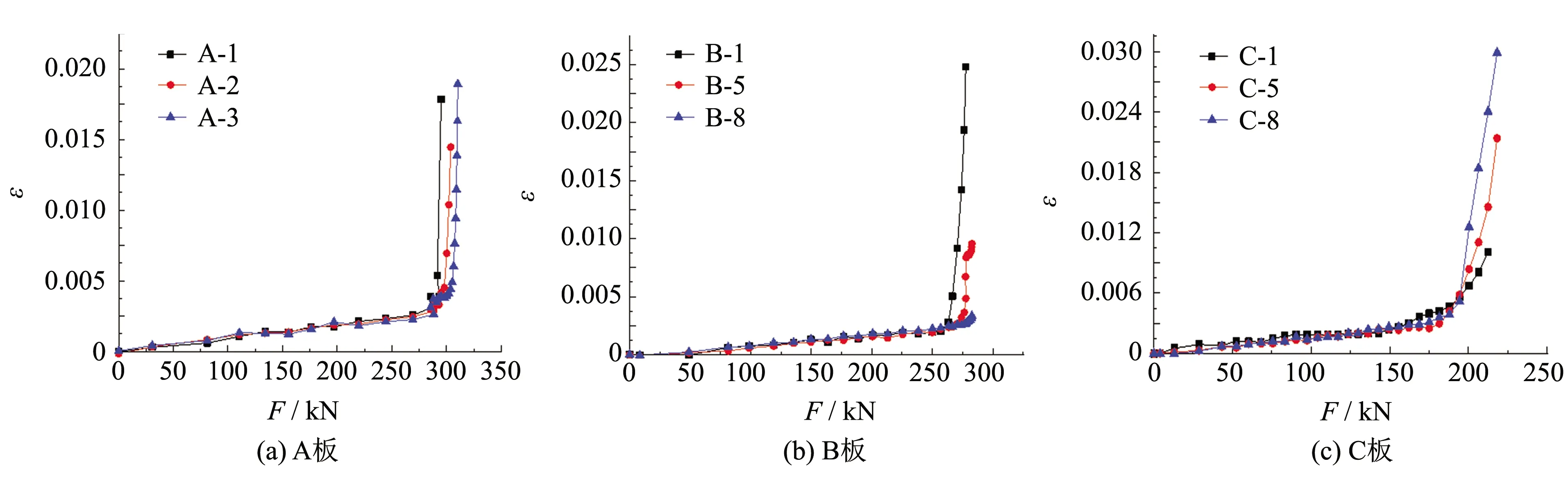
图7 不同宽板焊缝上侧应变分布对比图Fig.7 Comparison of strain distribution of different width plates along the upper side of the weld

图8 不同宽板焊缝下侧应变分布对比图Fig.8 Comparison of strain distribution of different width plates along the underside of the weld
从图7~8可看出,不同宽板焊缝上、下侧截面点位的应力应变在轴向拉力作用下,均呈现出先缓慢增加后快速上升的趋势. 对比不同宽板相同点位的上侧应变分布情况,A、B宽板1号点位均大于C宽板的1号点位,而C宽板8号点位在两端点位中应变变化范围较大,分析原因是局部的应力集中使宽板产生了较大塑性变形. C宽板5号点位应力应变比A、B宽板偏大,表明双点缺陷之间产生了相互作用,且相互作用对宽板受轴向拉力产生应变影响较大. 从宽板焊缝下侧应变可以看出,不同点位应变上升时间短,分析原因是焊缝下侧无缺陷分布,应力集中现象较少,但焊缝上侧缺陷仍对焊缝下侧应变分布产生影响.
3.4 缺陷处裂纹扩展分析
将A、B、C宽板的裂纹萌生位置、裂纹扩展路径、扩展长度lf和角度θ参数进行对比分析,如表3所示.
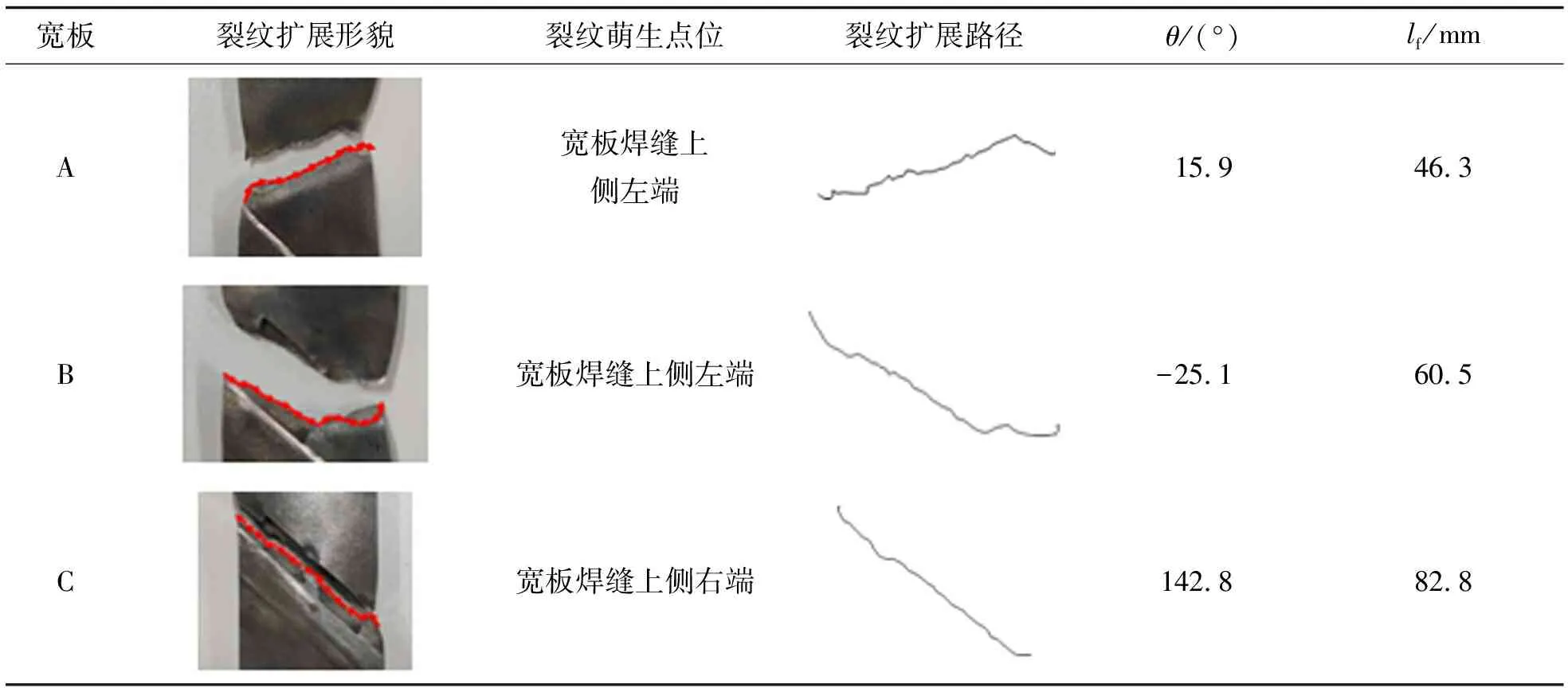
表3 焊缝处轴对称缺陷裂纹扩展参数表
结合焊缝上侧应变分析可知,A和B宽板裂纹萌生位置均在焊缝上侧最左端应变较大的1号点位,而含有双点缺陷的C宽板裂纹萌生位置在焊缝上侧最右端应变较大的8号点位,表明沿焊缝双点轴对称缺陷的相互作用对裂纹萌生产生了影响. 从宽板处裂纹扩展的扩展路径可以看出,A宽板颈缩现象较为明显,B宽板具有一定的颈缩现象,而C宽板的裂纹扩展路径较为平滑,且裂纹均沿着缺陷进行扩展. 从裂纹的扩展角度和长度看,A和B宽板较为相似,C宽板的扩展角度和长度均较大,说明双点轴对称缺陷对裂纹扩展产生了较大影响.
4 结语
1) 通过宽板模型研究缺陷处应力变化与裂纹扩展具有合理性, 且当缺陷相对长度为0.79(实际长度为20 mm),相对深度为45.98(实际深度4 mm)时,对裂纹萌生的影响较大.
2) 含缺陷宽板焊缝上、下侧截面点位的应力应变在轴向拉力作用下,均呈现出先缓慢增加后快速上升的趋势. 焊缝上侧点位中,由于局部的应力集中使宽板产生较大塑性变形,A、B宽板1号点位均大于C宽板的1号点位,而C宽板8号点位在两端点位中应变变化范围较大. 焊缝下侧不同点位应变上升时间短,应力集中现象较少,但焊缝上侧缺陷仍对焊缝下侧应变分布产生影响.
3) 拉应力作用下A和B宽板裂纹萌生位置均在焊缝上侧最左端应变较大的1号点位,C宽板由于双点缺陷的相互作用,裂纹萌生置在焊缝上侧最右端应变较大的8号点位. A和B宽板扩展路径、扩展角度、裂纹长度相似,单个缺陷对裂纹扩展影响较小,C宽板扩展路径平滑,扩展角度和裂纹长度均较大,双点缺陷相互作用对裂纹扩展产生了较大影响.