基于ABAQUS二次开发的直升机桨根快速建模方法及应力分析
2023-09-14刘俊增曾玖海
刘俊增 曾玖海
摘 要:随着新构型直升机技术的发展,对直升机桨叶有限元仿真技术的要求也越来越高。参数化建模仿真方法能够降低有限元法仿真技术的使用难度,对桨叶快速化、精细化设计具有重要意义。本文基于ABAQUS二次开发方法构建了一种适用于直升机桨叶根部段的快速建模方法,在有限元建模过程中参数化建立材料属性和接触属性,完成直升机复合材料桨叶根部段的快速化仿真分析。利用该方法对某直升机桨根进行应力计算,与常规建模方法相比,快速建模方法有效提高了建模效率,保证了仿真结果的一致性。快速建模方法仿真结果与常规建模方法仿真结果相比应变误差不超过1%,快速建模方法与试验结果相比应变误差不超过10%,常规建模与试验结果应变误差不超过91%,验证了该方法的可靠性。
关键词:直升机; 复合材料桨叶; 二次开发; 快速建模方法; 建模效率
中图分类号:V215.5 文献标识码:A DOI:10.19452/j.issn1007-5453.2023.05.010
旋翼桨叶是直升机的关键动部件,复合材料占比成为桨叶先进性的主要指标之一,先进直升机桨叶基本采用复合材料设计[1]。Z9、贝尔-214、AH-64D等直升机均在桨叶上使用了玻璃纤维复合材料或碳纤维复合材料,以增强桨叶的力学性能[2]。
复合材料的应用降低了桨叶重量(质量),大幅度提升了桨叶飞行寿命,但也给桨叶强度设计带来了新的困难,主要表现为其结构复杂,易产生应力集中、分层等问题,尤其是直升机桨根,它主要由蒙皮、大梁、填块、加强肋、填充物等部件组成。其应力分析方法主要包括工程梁算法和有限元法[3]。工程梁算法简洁高效,能快速进行模型重建和应力分析,但由于工程梁理论具有局限性,其应用范围受到较大限制。有限元法因其应用范围广,可对模型进行精细的分析而获得青睐。在直升机桨叶参数化建模方面,国外学者Ceil等[4]使用了参数化方法建立了单闭室和双闭室的剖面结构模型。S. Moffatt等[5]在BERP IV桨叶基础上使用了参数化方法建立了满足气弹剪裁要求的桨叶参数化模型。国内学者杨建灵等[6]为提高桨叶结构设计效率,以C形梁为研究对象提出了基于参数化组件定义的桨叶结构优化设计方法。赵秋华[7]在杨建灵的研究的基础上进一步讨论了桨叶接头填块、大梁和后缘条的参数化定义方法。这些方法推进了桨叶设计技术的发展。在直升机桨叶参数化有限元仿真方面的相关研究较少,有许多学者通过ANSYS、ABAQUS、NASTRAN等软件对复合材料桨叶进行了分析,获得了精确的桨叶强度仿真结果,但都采用了常规的有限元手动建模方法,建模效率低,不利于迭代设计,且分析结果会因人为因素产生差异[8-11]。
近年来,随着共轴高速直升机、双复合推力高速直升机等新构型直升机技术的发展,使用的复合材料占比越来越高,对桨叶有限元仿真技术的要求也越来越高[12-14]。但是在直升机桨叶实际设计过程中,往往需要多次迭代进行有限元建模计算,有限元法因繁琐的建模过程而在实际工程应用上受到较大限制。参数化建模仿真方法能够降低有限元法仿真技术的使用难度,提高桨叶迭代计算效率,对桨叶快速化、精细化设计具有重要意义。
为解决常规有限元建模方法耗时长、效率低的问题,本文建立了一种适用于直升机桨叶根段的快速建模方法,该方法基于ABAQUS平台,利用PYTHON开发接口,实现对桨根模型的快速建模,并对某直升机桨根进行应力分析,验证了该方法的可靠性。
1 桨根结构
桨根是桨叶结构受力状态最复杂的部位[3],桨叶的动载荷和静载荷通过根段传递到桨毂。复合材料桨根典型几何模型如图1所示,横剖面如图2所示,主要包括大梁、蒙皮、加强肋、泡沫等。

桨根组成部件中,蒙皮由0/90预浸碳布和预浸玻璃布铺设成形,可以起到定型和传力作用,对扭转刚度和摆振刚度贡献很大。大梁是桨根的主要承力部件,主要使用沿展向的碳纤维/环氧树脂基与玻璃纤维/环氧树脂基两种复合材料。蒙皮和大梁均为有限元仿真过程中的重点关注部件。
填块和泡沫使用质轻的短切纤维和硬质泡沫,主要起到支撑和固定作用。本文中采用的模型各部件材料见表1。
2 基于二次开发的桨根有限元建模方法
通过编写内核程序自动执行人工操作过程中重复性任务,可快速实现用户在前处理阶段的仿真建模过程,便于对建模过程进行修改和参数化分析[15-17]。
由于桨根结构复杂,在有限元建模过程中,建立材料属性和接触属性两個部分操作耗时最长。本文通过总结桨根几何模型的特性,构建了一种适用于直升机桨根段的快速建模方法,可以自动建立材料属性和接触属性,有效简化建模步骤,同时可以避免复杂操作过程中产生的建模错误。
2.1 自动建立材料属性
桨根组成部件中,蒙皮由多层复合材料铺设而成,在有限元模型中多用壳单元来表示,建立其材料属性最为繁琐;而在实际工程设计中,蒙皮多用参数化方法来描述,见表2,剖面位置是指沿桨叶展向方向,剖面位置到桨毂中心的距离,扭转角度是指桨叶全局坐标系到剖面局部坐标系的扭转角度,扭转中心是指在弦线上距剖面前缘的距离,一般为0。起点和终点坐标表示铺层起点与终点距前缘的距离, I、E分别代表上、下翼面,如图3所示。

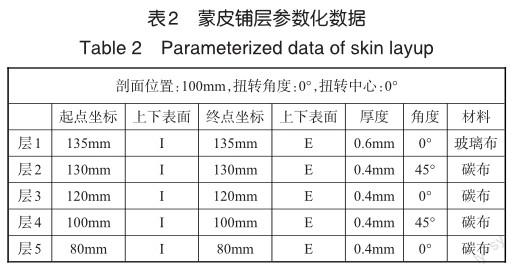
内核程序首先对蒙皮参数化数据进行读取,通过判断各层的起点及终点坐标位置分析蒙皮是否存在加强布以及加强布与其他铺层之间的相互关系。在内核程序中定义的常见铺层类型如图4所示,其中,图4(a)为不含加强布的常规铺层类型,图4(b)为不含加强布在相同位置铺层大于等于两层的类型,图4(c)~图4(f)为加强布在相对其他铺层不同位置的4种类型,图4(g)为既含有加强布又存在相同位置铺层大于等于两层的类型。
内核程序确定蒙皮铺层类型之后,读取蒙皮模型的几何特征,获取其所有面上的节点坐标,并将每个面沿桨叶展向坐标与弦向坐标值最大的节点作为特征点与该面一一对应。
分析所有特征点的坐标,根据桨叶展向坐标筛选出在目标剖面的特征点,通过桨叶厚度方向坐标区分上下翼面,并根据桨叶弦向坐标排序并编号,上翼面坐标排序示意图如图5所示,其中①~⑤代表层1到层5起点坐标,⑥代表前缘坐标。
根据蒙皮铺层类型确定每一层铺层的起始点与终止点,并赋予特征点对应几何面相应的材料属性,完成蒙皮材料属性的自动建立,如图6所示。
桨根各部件除蒙皮外,均为实体单元。内核程序通过读取表1中各部件与材料的对应关系可直接为其他部件建立材料属性。
2.2 自动建立接触属性
桨根在正常使用时,各部件连接处只有微小的相对位移和变形,因此在有限元建模过程中,采用绑定约束连接各部件接触面对模型进行简化。绑定约束要求每个表面只能做一次从面,但手动选择绑定约束的主从表面操作较为烦琐,且容易发生过约束错误。
为避免以上问题[18-19],内核程序首先通过用户界面读取用户输入的部件,为方便理解,各部件一般按照从外侧指向内侧的顺序,如先由剖面上翼面和下翼面指向内侧,再从前缘和后缘指向内侧。
由于桨根局部结构微小特征较多,为搜索到所有面,内核程序首先为蒙皮划分尺寸较小的网格,并获取蒙皮上所有节点[20]。如图7所示,根据节点坐标利用ABAQUS内置的getClosest函数搜索剩余部件与蒙皮的接触面,根据模型精细程度设置好容差,将搜索结果作为主面,蒙皮所有表面作为从面,建立绑定约束。
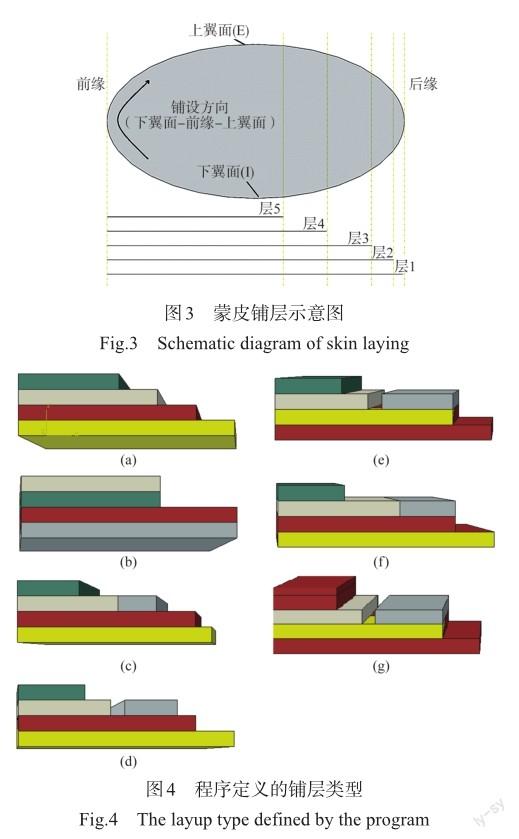
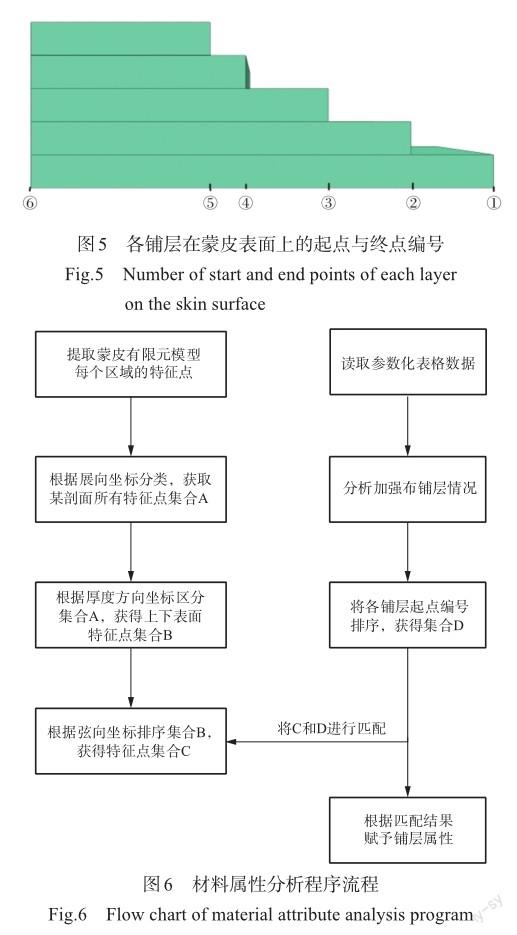
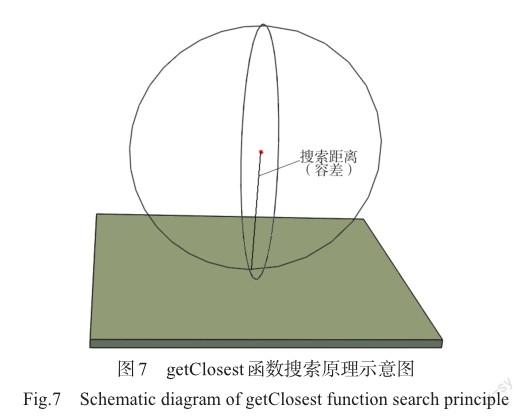
本文中内核程序根据用户输入顺序依次将蒙皮、大梁、肋、泡沫等部件表面作为从面,搜索结果作为主面,建立TIE约束,完成桨根接触属性的建立,其流程如图8所示。

3 桨根强度分析
使用常规建模方法和本文的快速建模方法完成某型号桨叶根段的建模。将桨根连接处一侧固定,在另一侧建立参考点与桨根关注区域右侧剖面耦合,并在参考点分别施加挥舞力和摆振力,如图9所示。

图10和图11分别为采用快速建模方法和常规建模方法时挥舞应变和摆振应变仿真结果与试验结果的对比图,对比分析可知,快速建模方法仿真结果与常规建模方法仿真结果的挥舞和摆振应变误差不超过1%,快速建模方法仿真仿真结果与试验结果应变误差在-10%~8.3%之间。常规建模方法仿真结果与试验结果应变误差在-9.1%~9%之间,证明了快速建模方法的可靠性。

4 结论
针对直升机桨叶根段仿真建模繁琐、耗时长、不利于迭代等问题,本文基于ABAQUS二次开发构建了桨根快速建模方法,可以自动建立桨根有限元模型的材料属性和接触属性,并通过对比某型号直升机桨根的快速建模方法仿真结果、常规方法仿真结果和试验结果,验证了该方法的可靠性。
在桨根有限元建模过程中,常规的建模方法在定义材料属性和接触属性时虽然因模型复杂程度用时不同,但多数耗时超过1h,而快速建模方法耗时一般不超过5min。快速建模方法有效解决了在桨根迭代设计过程中有限元建模的效率问题,并通过固定的程序逻辑避免了复杂操作过程中产生的建模误差,保证了仿真结果的一致性。
参考文献
[1]黄文俊,李满福.直升机旋翼设计技术应用现状及发展综述[J].航空制造技术,2011(17):32-35. Huang Wenjun,Li Manfu.Application and development of rotor design technology for helicopter[J].Aeronautical Manufactur‐ing Technology,2011(17):32-35.(in Chinese)
[2]孟雷,程小全,胡仁伟,等.直升机旋翼复合材料桨叶结构设计与选材分析[J].高科技纤维与应用,2014,39(2):16-23. Meng Lei, Cheng Xiaoquan, Hu Renwei, et al. Material selection in helicopter composite blade structure design[J]. Hitech-Fiber and Application,2014,39(2):16-23.(in Chinese)
[3]程小全,高宇劍.含穿透损伤复合材料桨叶结构静强度分析[J].失效分析与预防,2011,6(1):23-27. Cheng Xiaoquan,Gao Yujian.Static analysis of composite rotor blade with penetration damage[J].Failure Analysis and Preven‐tion, 2011,6(1): 23-27.(in Chinese)
[4]Celi R. Aeroelastic modeling of swept tip rotor blades using finite elements[J]. Journal of The American Helicopter Society, 1988, 33(2) : 43-52.
[5]Moffatt S,Griffiths N.Structural optimisat Ion and aeroelastic Tailoring of the berp IV demonstrator blade[C]. American Helicopter Society 65th Annual Forum, 2009:15-20.
[6]杨建灵.基于整体参数化定义的直升机桨叶结构设计与优化[D].南京:南京航空航天大学,2013. Yang Jianling.Structure design and optimization for helicopter blade based on global parametric definition[D]. Nanjing: Nanjing University of Aeronautics and Astronautics, 2013.(in Chinese)
[7]赵秋华.直升机桨叶结构参数化几何建模与剖面特性分析技术研究[D].南京:南京航空航天大学,2015. Zhao Qiuhua. Researches on parametric geometry modeling and profile characteristics analysis for helicopter blade structure[D]. Nanjing:Nanjing University of Aeronautics and Astronau‐tics, 2015.(in Chinese)
[8]杨文志,朱锡,陈悦,等.复合材料螺旋桨纤维铺层对强度影响研究[J].舰船科学技术,2016,38(3):85-90. Yang Wenzhi, Zhu Xi, Chen Yue, et al. Research for the ply intensity on the strength of composite propeller[J].Ship Science and Technology,2016,38 (3):85-90.(in Chinese)
[9]José P B, Christian B, Poul A. Hydro-elastic analysis and optimization of a composite marine propeller[J]. Marine Structures, 2009,23(1):22-38.
[10]尚丽娜.重型直升机及旋翼桨叶加筋薄壁结构设计[D].南京:南京航空航天大学,2009. Shang Lina. Structural analysis of stiffened thin walled rotor blade for heavy-lift helicopter [D].Nanjing: Nanjing University of Aeronautics and Astronautics,2009.(in Chinese)
[11]李雪芹,陈科,刘刚.基于ANSYS的复合材料螺旋桨叶片有限元建模与分析[J].复合材料学报,2017,34(4):591-598. Li Xueqin, Chen Ke, Liu Gang. Finite element modeling and analysis of composite propeller blade on ANSYS[J]. Acta Materiae Compositae Sinica,2017,34(4):591-598.(in Chinese)
[12]邓景辉.直升机技术发展与展望[J]. 航空科学技术,2021,32
(1):10-16. Deng Jinghui. Development and prospect of helicopter technology[J].Aeronautical Science & Technology,2021,32(1): 10-16.(in Chinese)
[13]吴希明,张广林,牟晓伟. 中国直升机产业的现状及发展建议[J].航空科学技术,2021,32(1): 3-9. Wu Ximing, Zhang Guanglin, Mu Xiaowei. China helicopter industry status and develo- pment proposal[J]. Aeronautical Science & Technology,2021,32(1):3-9.(in Chinese)
[14]李春华,樊枫,徐明.共轴刚性旋翼构型高速直升机发展研究[J].航空科学技术,2021,32(1): 47-52. Li Chunhua, Fan Feng, Xu Ming. Development of high-speed helicopter with coaxial rigid rotor configuration[J]. Aeronautical Science & Technology, 2021,32(1):47-52. (in Chinese)
[15]石亦平,周玉蓉. ABAQUS 有限元分析實例详解[M]. 北京:机械工业出版社,2006. Shi Yiping, Zhou Yurong. Detailed explanation of ABAQUS finite element analysis example [M]. Beijing: China Machine Press,2006.(in Chinese)
[16]曹金風,王旭春.Python语言在Abaqus中的应用[M].北京:机械工业出版社,2011. Cao Jinfeng, Wang Xuchun. The application of Python language in Abaqus[M].Beijing:China Machine Press,2011.(in Chinese)
[17]霍永强,李言,崔莅沐,等.ABAQUS二次开发在冷滚打成形参数化建模与仿真研究中的应用[J/OL].机械科学与技术:1-12.https://doi.org/10.13433/j.cnki.1003-8728.20220100 Huo Yongqiang, Li Yan, Cui Limu, et al. Application of ABAQUS secondary development in parametric modeling and simulation of cold roll-beating forming[J/OL]. Mechanical Science and Technology for Aerospace Engineering:1-12.https://doi.org/10.13433/j.cnki.1003-8728.20220100.(in Chinese)
[18]刘湘云,赵荃.开孔复合材料层压板剩余强度分析建模ABAQUS二次开发[J].机械设计与制造工程,2019,48(12): 29-32. Liu Xiangyun, Zhao Quan. The secondary development of ABAQUS for residual strength of open-hole composite laminates[J]. Machine Design and Manufacturing Engineering, 2019,48(12):29-32.(in Chinese)
[19]吴航.ABAQUS二次开发在顶管开挖面分析模拟中的应用[J].建设科技,2021(11):101-104. Wu Hang.Application of ABAQUS secondary development in analysis and simulation of pipe jacking excavation[J]. Construction Science and Technology, 2021(11): 101-104. (in Chinese)
[20]安康. ABAQUS二次开发在基于网格的变形几何体重构中的应用[D].兰州:兰州理工大学,2020. An Kang.Application of ABAQUS secondary development in mesh based deformation geometry reconstruction[D].Lanzhou: Lanzhou University of Technology,2020.(in Chinese)
Rapid Modeling Method and Stress Analysis on Helicopter Propeller Root Based on ABAQUS Secondary Development
Liu Junzeng, Zeng Jiuhai
China Helicopter Research and Developent Institute,Tianjin 300300,China
Abstract: In order to improve the modeling efficiency of helicopter composite propeller root and ensure the consistency of simulation results, based on ABAQUS secondary development method, a rapid modeling method for helicopter propeller root segment is constructed in this paper, which can quickly establish material properties and contact properties in the process of finite element modeling. This method is used to calculate the stress of a helicopter propeller root. Compared with the conventional modeling method, the rapid modeling method can improve the modeling efficiency effectively. The strain error of the simulation results of the rapid modeling method is less than 1% compared with the simulation results of the conventional modeling method, and less than 10% compared with the experiment results, which verifies the reliability of the method.
Key Words: helicopter; composite blade; secondary development; rapid modeling method; modeling efficiency